In 2003 I was trying to think of ways to make the bronze that I loved into a lighter form – something that was bronze and sculptural but that had a lightness to it – a floating quality. The idea of broken eggs was an inspiration. I made a wax model of an egg, very thin, and broke it at the top. This was the first model but the outside was too smooth and, well, egg like. So I tried some different textures and came up with a soft hammering that allowed the tones of the bronze to be revealed while keeping the egg form. It looked like a broken moon covered in craters.
The first bronze was cast but the edge was too thick and the bronze foundry said they could not cast it thinner. So I took a grinder and ground the inside away until I reached the outside – a very thin edge was formed. From this edge I could break away pieces to give a jagged, broken egg-shell look. Finally I had the form and the technique. Over the next year I sold the bowls without gilding. I liked the bowl being very dark – like a dark moon.
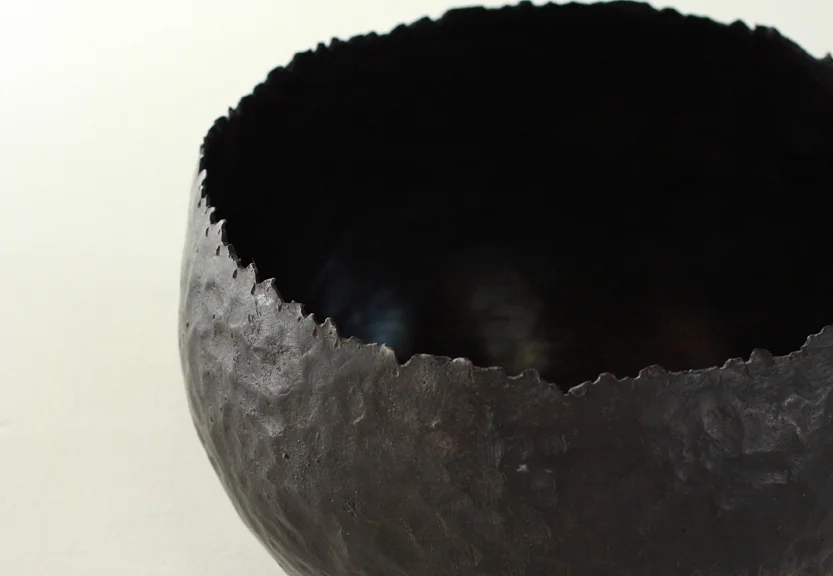
Then I thought of the idea of creating an eclipse with precious metal. Silver created a cool and ‘black/white’ contrast while gold brought a softer, warmer light and very beautifully exuded the idea of an eclipse in emanating light. It had taken about 2 years of drawing, model making, testing textures and patinas, gilding and finally trying the bowl in many different sizes before settling on seven that had the perfect texture and form and that worked well together. Of these seven, I found that three bowls had the perfect size and form – and these have been the best sellers for the past years.

In 2005 I entered the perfected design in a craft and design competition created by UNESCO. Their goal was to encourage innovation and design in traditional materials and we won this award. The story of how I designed, developed and produced these bowls shows how even a very simple design takes effort and thought in its development to achieve the right result. It starts with imagination and inspiration and then becomes a technical pursuit of new finishes and techniques such as the grinding technique to achieve the desired thinness. This process and the challenges that define it are at the heart and soul of my company. We are small and innovative and working in beautiful but also complex materials. It is a privilege to work with these materials and methods and moments of great satisfaction, like seeing the first Hammered Bowl, are the reward.
Several companies have produced copies of my Hammered Bowl designs. From what I can see these copies are mostly made of thin iron painted to look like copper so that when you lift them up they feel lightweight and insubstantial. They have a hammered pattern that is rough and too uniformly applied and the colour inside is spray-on fake gold paint. I feel that the company that copies always misses the heart and the beauty of the original. This is because they didn’t have the idea, they didn’t go through the development or experience the excitement of seeing something born from their own ideas. This struggle and pursuit of quality and innovation is why some companies are started. I want to make things that have the idea wrought into the piece, things that exude the hard won inspiration. We cannot stop other companies from copying our designs but we can stand for everything that is opposite to the ethics of mass production and creative shortcuts.
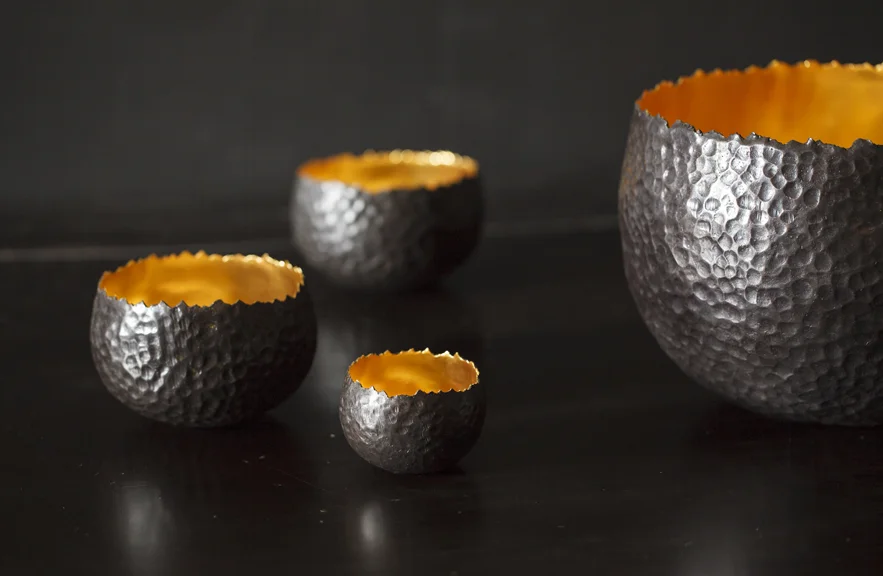