Its been some time since I told the story of one of my designs. Part of this years Intarsia collection of furniture and lighting is the Wishbone Table Raised on bronze legs it has a top covered in a special combination of materials.
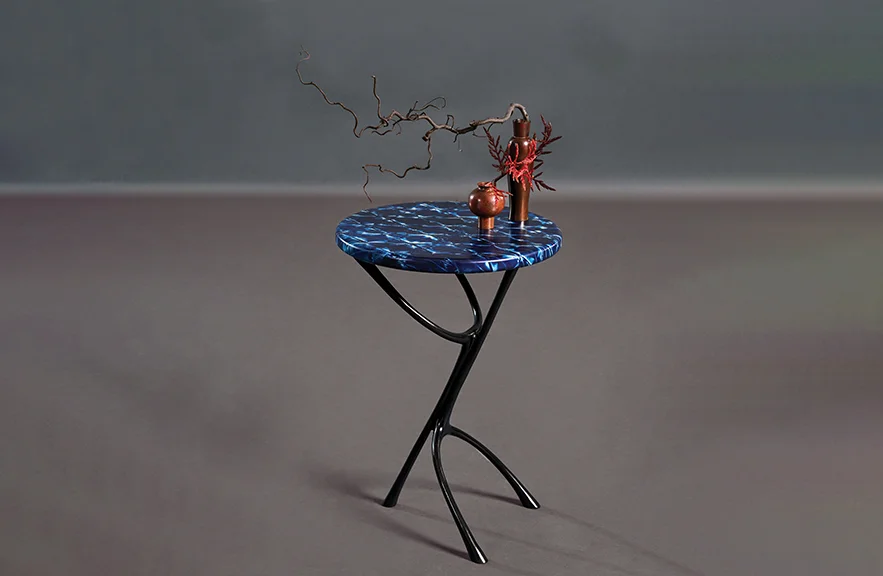
I was sketching a wishbone – proper name the furcula, which are the forked fused-clavicles unique to birds. I was stretching the form; simplifying and exploring it, which I do with something I like – looking for a way to bring it into a design. Working with a soft pencil and a nice sketch pad to find lines and think through structural ideas will never be beaten by any computer-based drawing suite. I wasn’t trying to draw tables but the shape suddenly appeared as legs!
During the sculpting in wax of those legs I worked on the weight and balance and shaping of the feet.
There were a number of ideas for the material to use on the table top; lacquered spun bamboo, verre eglomize, lacquered straw… Then the first trials of a new parchment dyed in natural indigo were finished and I decided to use this because part of the inspiration for Intarsia had been the iridescence of butterfly wings. Parchment is not an iridescent material but the varied effect of the indigo – how it stains deeply the most exposed areas and lightly floods other areas in a spectrum of blues – on the folded goatskins, was as close to it as can be achieved on this material.
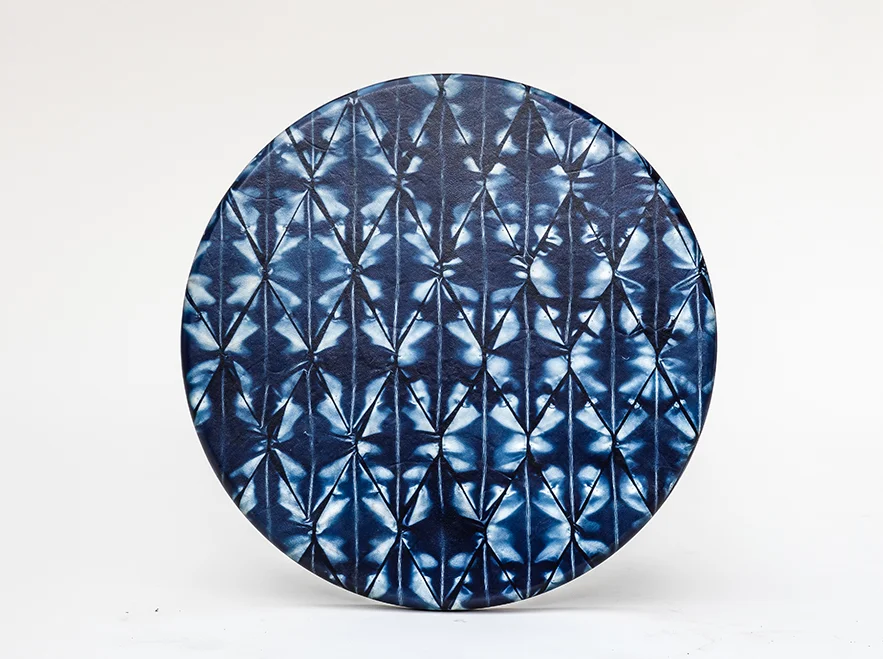
To use shibori (the Japanese method of folding and tie-dyeing) with parchment is a tough job. We have to fold the thick skin very accurately and then sew it tightly. If the tension varies too much then you have much darker or lighter spots. Finding a pattern that reminded us of a butterfly took many trials.
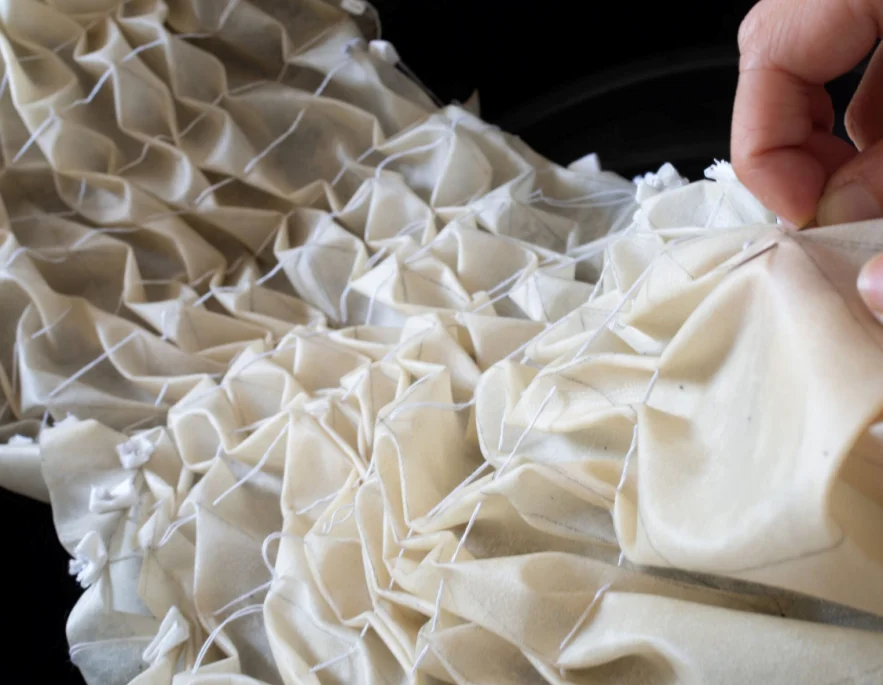
Indigo dyeing in Asia uses the plant indigofera tinctoria. It is one of natures rare blue organic compounds. It has a special place in East Asia as a dyestuff for minority peoples clothing and all manner of textiles and of course carpets.
Indigo dyeing requires skill and patience. Mature leaves are taken only from stems that have pods attached. In Thailand these are then soaked to create a paste that is mixed with precise amounts of quicklime, rice wine, crushed citrus leaves and ash water from burnt coconut trees. This heavier paste is then left to ferment and the process takes a few days to produce cakes of natural deep blue dye-stuff.
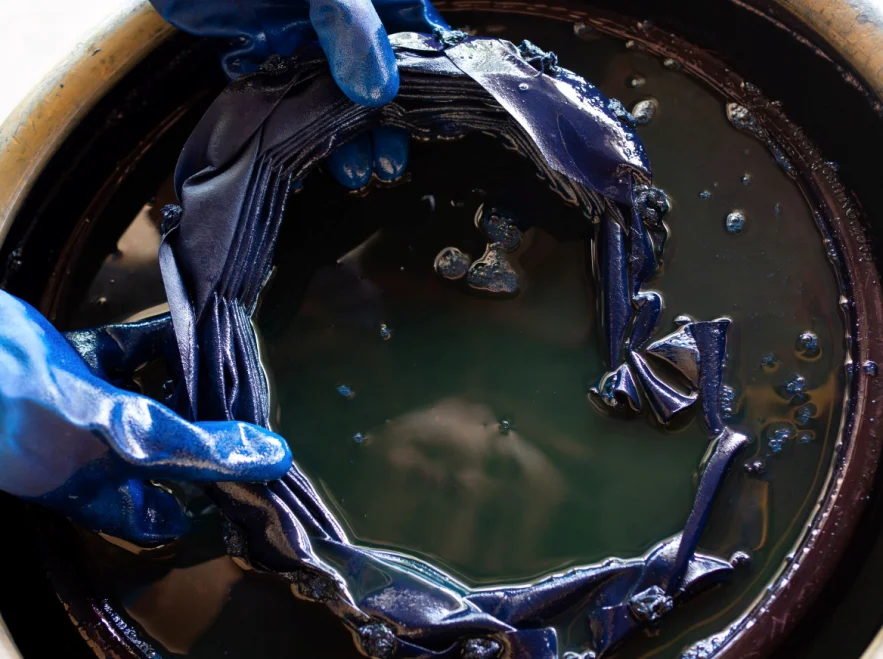
To work with the dye, a material or yarn is put into a bath made from these fermented cakes, however, the actual colouring only occurs through oxidization as the material is removed and meets the air. Different from most dyes that corrode in one way or another, indigo coats the object with colour. This has the effect of making the final material much stronger than it was before and explains why so many peoples prefer to live their lives clothed by this ruggedly beautiful colour that also happens to fade and grow more beautiful over time as the cloth softens.
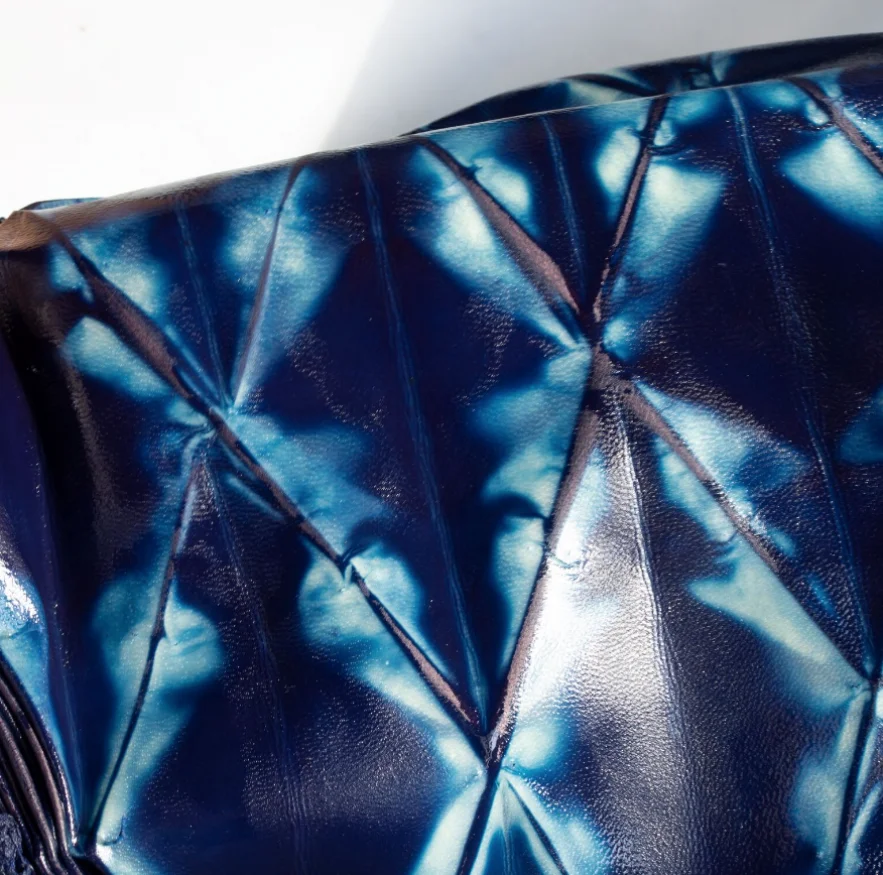
In principle the indigo dye process is simple, but in practice it takes great skill to achieve deep blue tones. In many societies, from Central Asia to Indonesia, the dyeing techniques are a closely guarded secret of specialist craftspeople. Collecting the leaves at their best; creating the fermented paste; adding exact proportions of additives; the temperature and humidity at the time of dyeing… like great bread, it is a job that requires many factors to achieve success.
For thousands of years indigo has been known about and widely used. Today however it is rarely found, so it has been a pleasure to work with it in an innovative way and combine it with the Japanese method of shibori, or tie dye.
The table is a ‘typical’ Alexander Lamont piece; a striking blend of traditions and techniques from East and West, including bronze casting, parchment inlay, indigo dyeing, shibori tie-dye and wood veneering. No two pieces are the same but all are made with great passion and attention to detail.
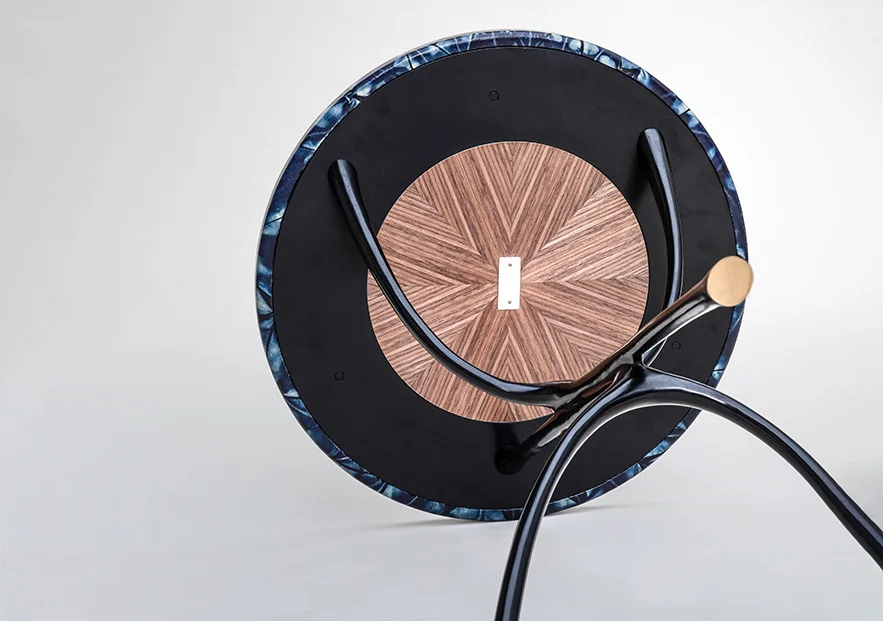