Strong, yet flexible, bronze is a sculptural material that has been employed in the decorative arts of Europe, Africa and Asia for millennia. In fact, one of the first craftsmen Alex worked with in Thailand was a bronze caster from Chiang Mai, a master of the lost wax method traditionally used for Buddha sculptures. Together Alex and the bronze caster made the first piece: a bronze bowl encrusted with the coils that cover the head of the Buddha. As Alex recounts, “there was something monumental and primordial about the mass of bronze that flowed to make this vessel.”
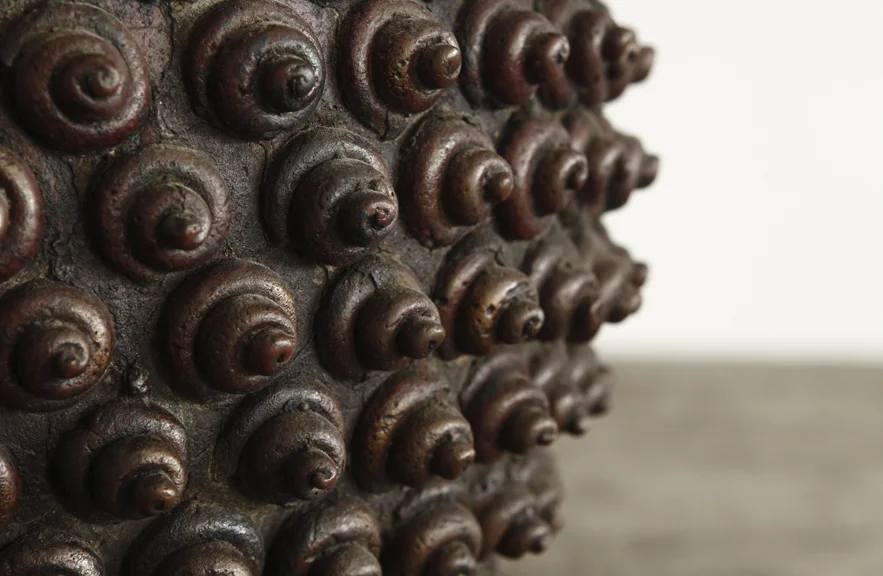
The first bronze vessel Alex developed, inspired by the coils seen on the head of the Buddha.
Lost-wax casting requires a model of the piece to be made in wax. The wax model is covered with ceramic clay, dried and heated. The wax melts and pours out (is lost) through flues, leaving a cavity the same as the original wax. Molten bronze is poured into the cavity. The flues act as drains and avoid pressure build-up, allowing the bronze to fill the space. The clay is broken and a bronze model remains that requires arduous sanding, chasing and finishing.
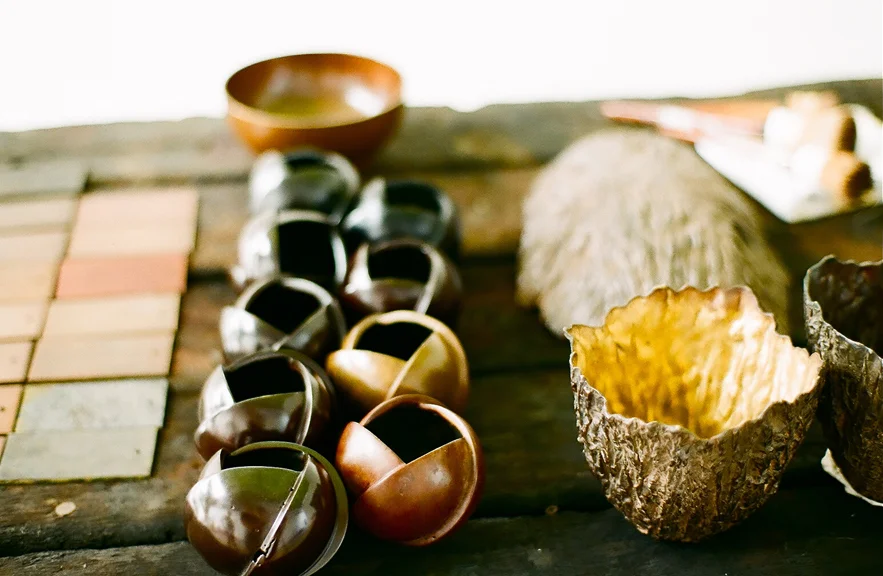
Alexander Lamont bronze workshop.
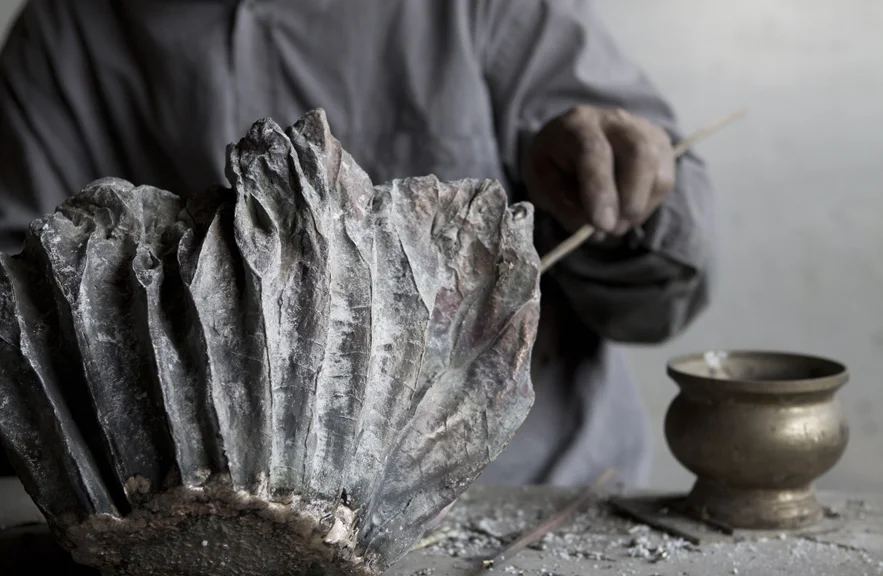
Craftsman in the bronze workshop.
At Alexander Lamont all our models and molds are made in-house and we work in both bronze and brass depending on the item. They are different because of the relatively higher copper content in bronze. This makes bronze slightly softer and a tone darker than brass. Patinated brass is often preferred to bronze as a base material due to its relative strength and the resulting ability to create thinner, lighter pieces. Whatever the copper alloy, we achieve our desired quality partly through the base material but mainly through the control of the modeling, mold-making and patination.
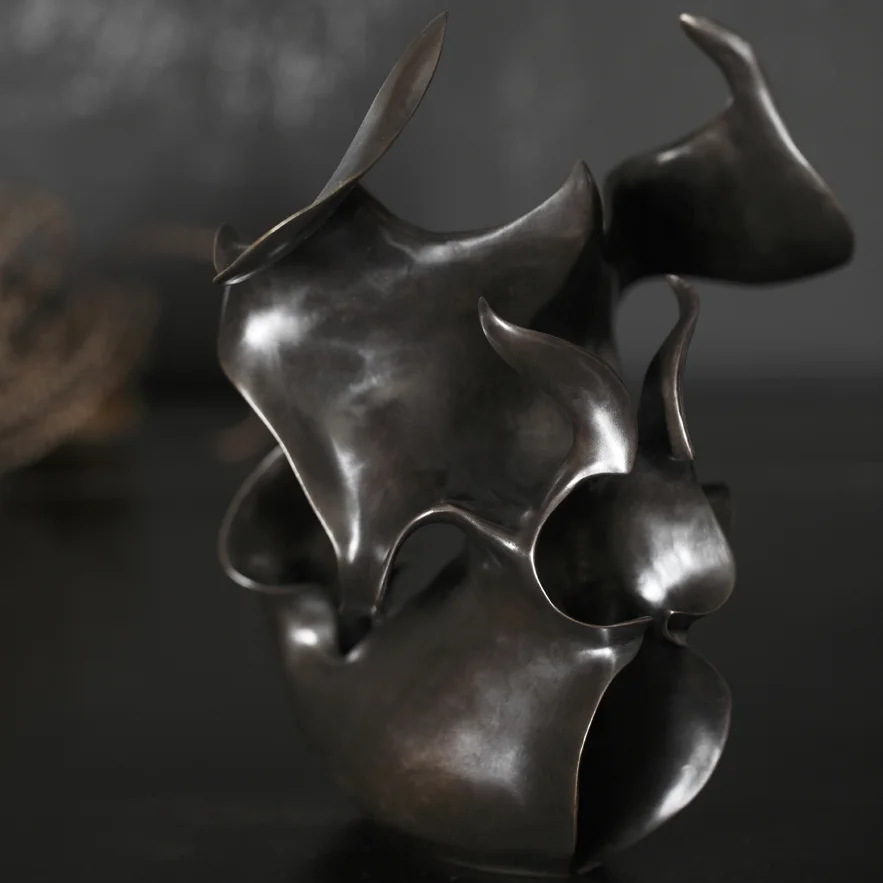
Encyclia vessel from the Black Orchid Collection
As part of the finishing process, we apply various patinas to our brass/bronze products in order to achieve the desired colour and finish. Our patinas are applied by hand and display variations in tone and colour.