As we may have mentioned before, it is truly difficult to improve on nature. Natural wood is a thing of great beauty. The shades, textures, colours and dramatic lines and patterns that emerge from its figure can be all things from simple and linear to sublimely expressive, even explosive. The Egyptians certainly recognized this over 4,000 years ago. Wood, was so scarce in their desert home that it was regarded as a precious and rare commodity. In striving for the most intelligent use of their exotic logs, they became the first civilization to saw wood into thin boards, expanding its surface area substantially and thereby making the first known ‘veneers.’ These are evident in the tomb of King Tut where ebony veneer inlaid with ivory was discovered covering a cedar wood casket.
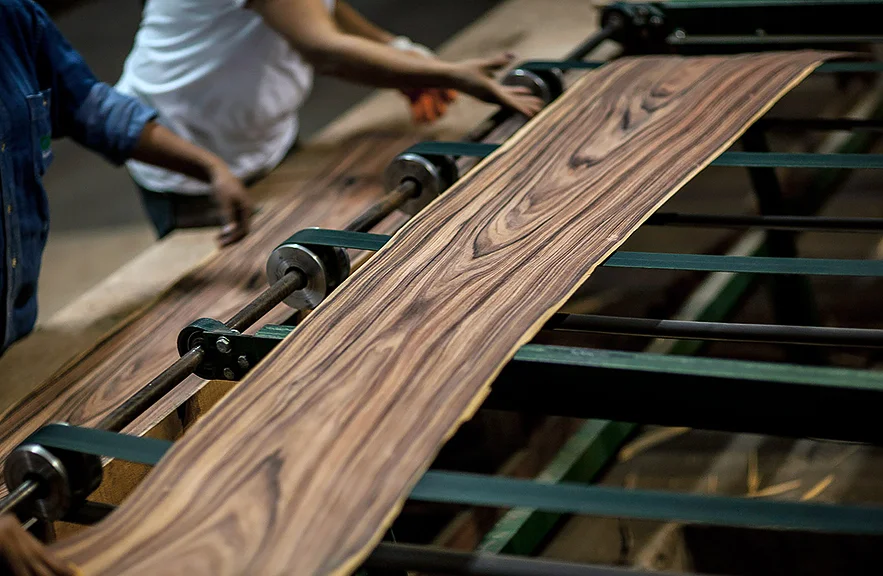
“Wood is still a precious material and we use it with great care.” says Alexander. “Solid wood with beautiful grain is often restricted to veneer production to maximize its useage. So it is important that we develop good veneering skills and access the best sources of wood veneer. Steven Lanham, Workshop Operations Manager adds : “We import some of the best, high quality wood sheet material out there.” Steven’s experience with wood goes back to his apprenticeship as a skilled cabinet-maker in England in the 1990’s. Since then he has worked in some of the highest quality woodshops in Europe and the United States. “The veneer we buy is hand-selected when purchased and then again when incorporated into the design. Veneer is given the same treatment and attention as all our other natural materials.”
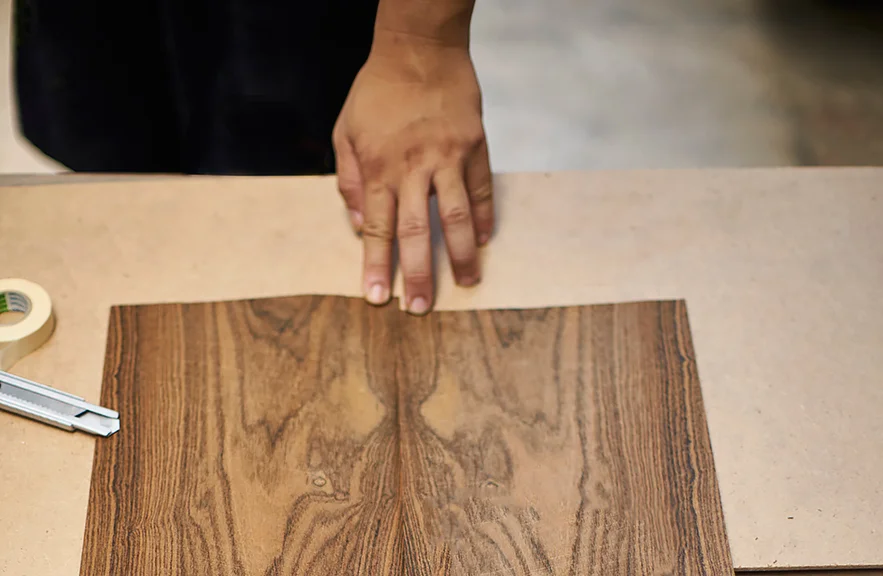
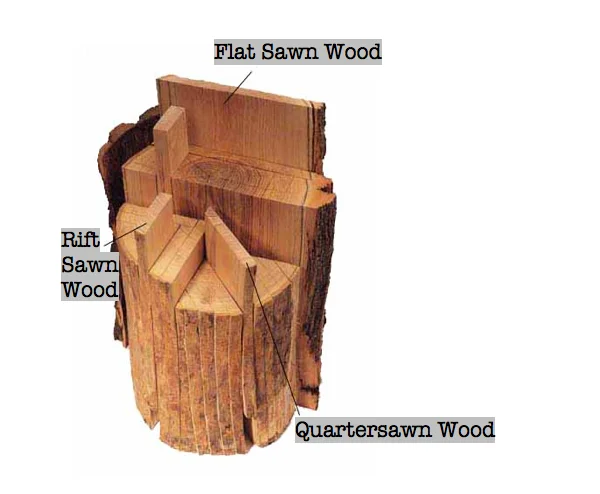
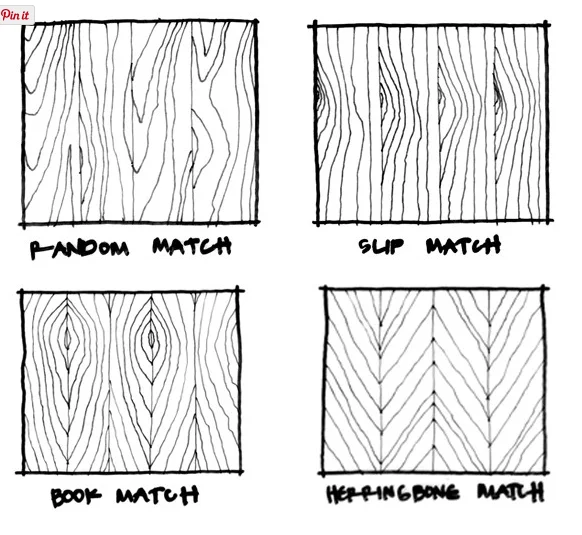
Veneer is often classified by its thickness and also by its figure (or grain as it’s commonly referred to), which depends on how the log is cut. Additionally, the way the veneer is matched adds an entirely different design perspective to a piece. It’s also vital that that the substrate used to apply the veneer is of a very high quality. “We would not apply any of our materials to locally sourced wood sheet – The wood and construction method results in a sub-standard sheet surface which transmits into a sub-standard piece of furniture,” says Steven. All Lamont’s wood materials – those used in the furniture, accessories and lamps they make – are imported from the West using northern hemisphere wood that is dry, pale-toned, simply grained and less oily than Asian materials. Veneer sheets are laid up by hand and then pressed by a veneer press.
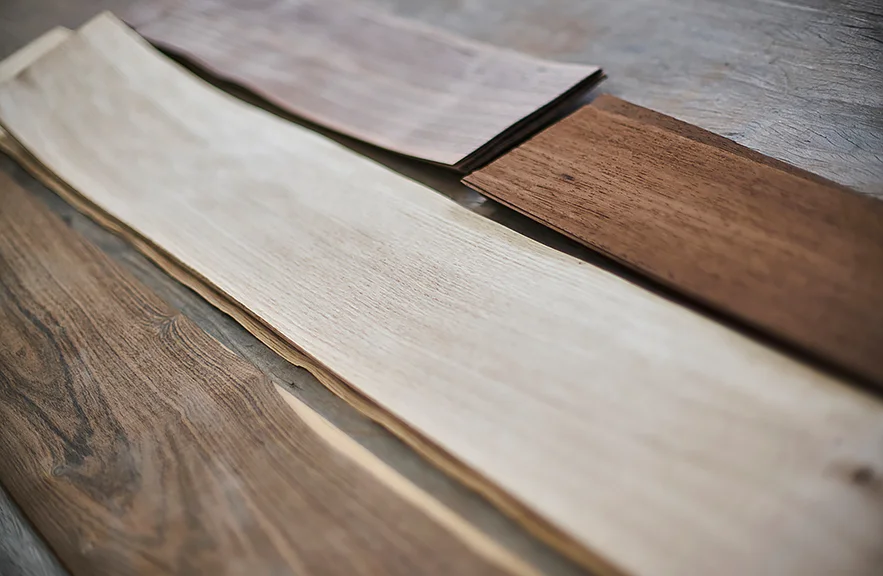
At the Alexander Lamont workshop we use many different species of veneer to provide the best compliment to the other natural materials on a particular piece. Oak and teak are used on our boxes because of their historical reference and simplicity, while Walnut provides an elegant and warm surface to the back and interior of the River Ledge Credenza and tables. This year we have incorporated Wenge and Louro Preto, both used in our Spring collection pieces.
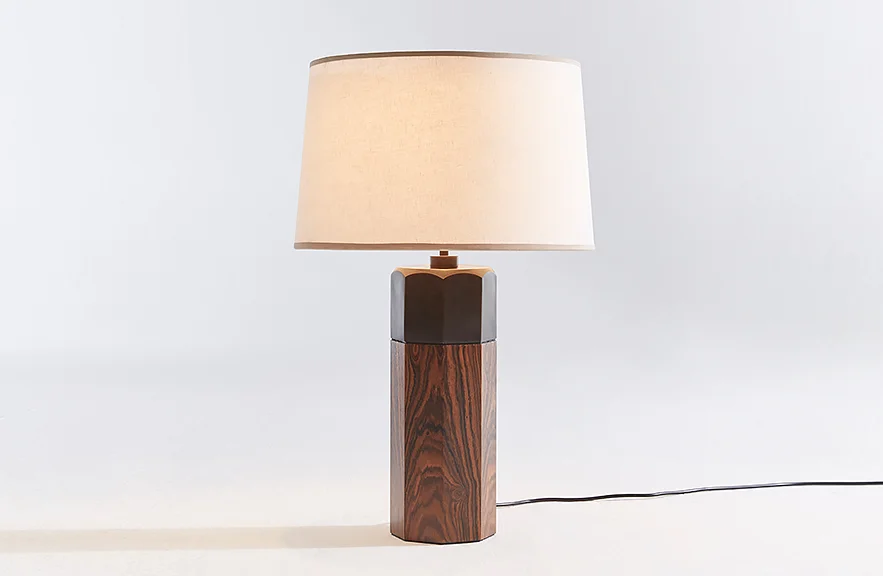
The new octagonal Otto Table Lamp showcases the dramatic figure of the Brazilian Louro Preto wood. The veneer is sliced in the “cathedral” cut, where the first bundles from a log are sliced across the center grain. The tall, dramatic arches of the dark wood are then polished and waxed to bring out their beauty and luster.
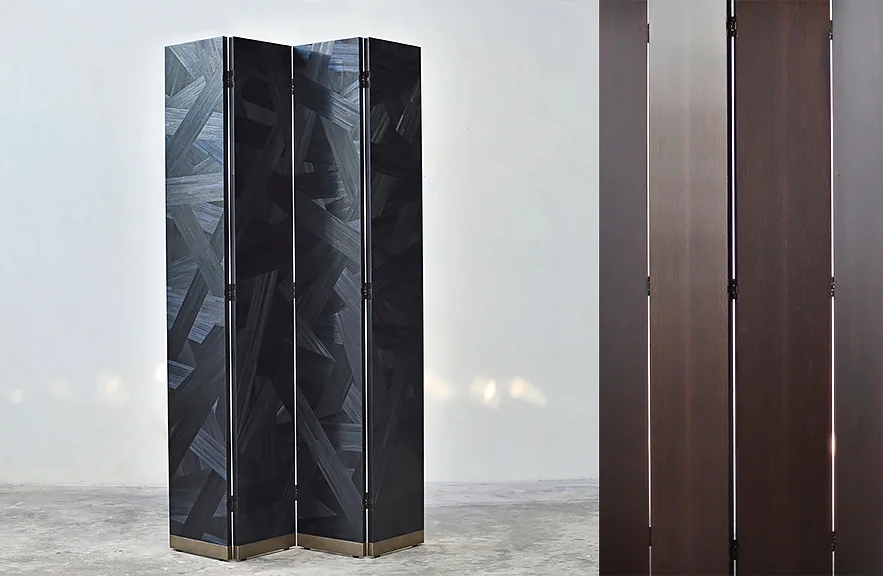
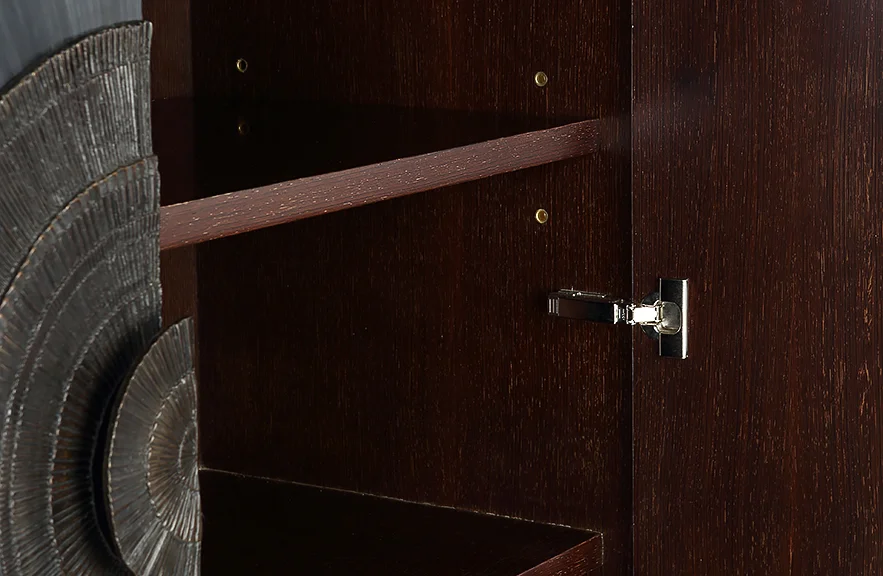
A large surface of Wenge is visible on the back of our new screens along with the interior of the Agata and Amadeo Cabinets. This elegant African hardwood was selected for it’s unique grain and dark beauty. Polished and sanded to refine its texture before being lacquered, wenge veneer brings a rich textured chocolate tone to the surface of larger pieces.
Using fine quality wood veneer on the underside, inside and back of our pieces, sometimes cut and positioned to dramatic effect, brings a refined finish to even the hidden areas of our pieces – a degree of detail described in the furniture industry as ‘360 degree luxury.’ Alexander prefers to describe it as “making things without any short cuts, rough edges or nasty surprises.”